
If the battery has a low charge, the PCM may use the engine to move down the road while communicating to the motor to go into power generation mode to charge the battery. If the battery is sufficiently charged, the PCM may signal the motor and related components directly or through specific controllers to drive the vehicle on pure electric power or in combination with the engine. For example, in a hybrid vehicle when the driver’s foot presses on the accelerator, various conditions such as battery charge and the amount of pedal depression determine what is controlled to move the vehicle down the road. However, in electrified vehicles this becomes more complicated. When this occurs the engine computer, known as the powertrain control module (PCM), receives input from sensors and increases the amount of fuel injected. An example of fuel control on a non-electric vehicle is when the driver’s foot presses on the accelerator. The controls of these components are performed through dedicated modules which communicate with each other to determine the correct control procedure for components.
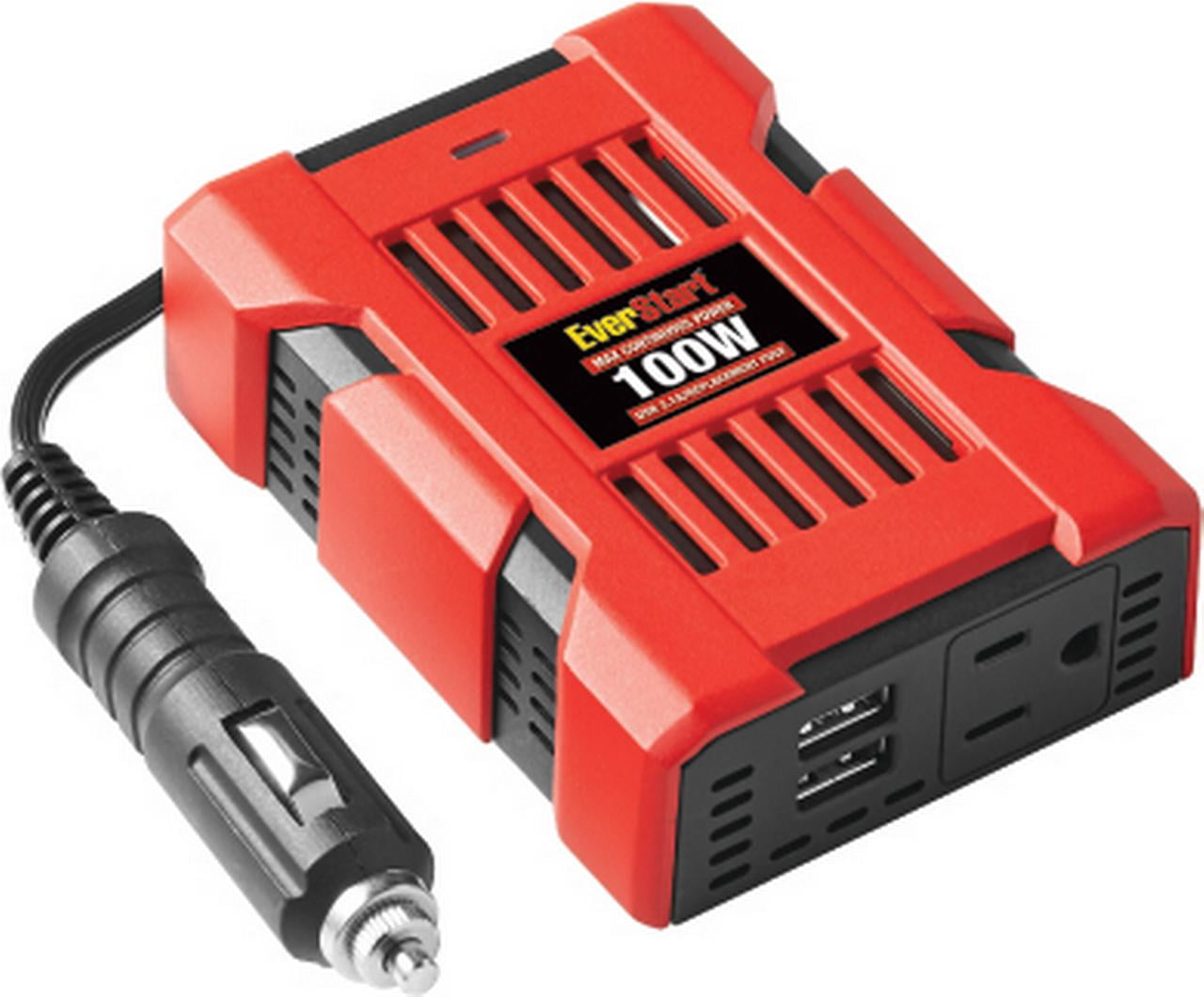
These components must be controlled for correct and efficient operation. Additional components of electrified vehicles include high voltage batteries, motors, inverters, converters, pumps, regenerative brakes, and additional accessories. ControlsĬontrol systems are a vital part of all automobiles and are more complex in electrified vehicles where additional components must be monitored and controlled appropriately. InvertersĬonverts direct current (DC) from the battery to alternating current (AC) to be used by other devices such as the traction motor and coolant pump. An application of a step down inverter would be decreasing the high voltage direct current (DC 180-300 volts) from the HEV/EV battery to low voltage (12-14 volts) DC that can be used to charge the 12 volt auxiliary battery and operate light load devices such as lighting, radio, and windows. An advantage of using a converter to increase voltage from the battery is a smaller and less expensive battery may be used while still utilizing an efficient high voltage motor. An application of a step-up converter is converting EV/HEV battery voltage (typically 180-300 volts) to about 650 volts to power the traction motor. In EVs/HEVs step-up and step-down converters are combined into one unit. A converter that increases voltage is called a step-up converter and a converter that decreases voltage is called a step-down converter. The "Voltec" powertrain control system used in the Chevy Volt ConvertersĪ device that increases or decreases the voltage (AC or DC) of a power source depending on application.
